Introduction
The world of manufacturing is going through a massive shift, thanks to the rise of Cyber-Physical Systems (CPS) and Smart Manufacturing. These cutting-edge technologies are transforming how we make products, manage supply chains, and even maintain machines. As we embrace Industry 4.0, it’s clear that the way we think about production is changing forever. So, what exactly are these systems, and how do they work together to make manufacturing smarter, faster, and more efficient?
Let’s dive in and explore the exciting world of CPS and Smart Manufacturing—you’re in for a technological treat!
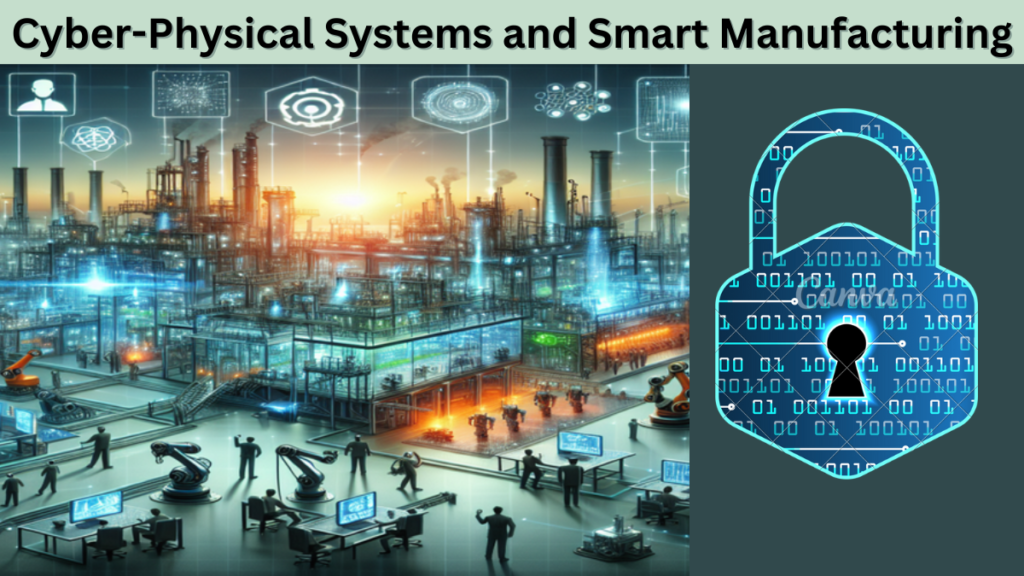
What are Cyber-Physical Systems?
Cyber-Physical Systems, or CPS, represent the fusion of the digital and physical worlds. Imagine a world where machines not only do what they’re told but also learn from the data they gather, adapt to their surroundings, and make decisions on their own. Sounds like sci-fi? It’s not! CPS are systems that tightly integrate computation, networking, and physical processes. In manufacturing, these systems are powered by sensors, robots, and real-time data analytics to enhance precision, speed, and adaptability.
Take, for example, a factory where robots are not only assembling parts but also collecting data from their environment, processing it, and adjusting their actions accordingly. These systems are connected to the internet, enabling them to interact with other machines and even predict when maintenance is needed. It’s like having a factory that can think, react, and evolve over time. By connecting these systems to each other, CPS helps manufacturers stay ahead of the curve by ensuring everything is operating at peak efficiency. Cool, right?
Smart Manufacturing: Key Components and Technologies
So, how does CPS fit into Smart Manufacturing? Well, smart manufacturing is all about using advanced technologies to make production processes more automated, flexible, and intelligent. And guess what? Cyber-Physical Systems are the backbone of it all! Think of Smart Manufacturing as a giant brain overseeing everything, from production lines to logistics. It incorporates several components, including AI, robotics, machine learning, and, of course, CPS.
In this brave new world, machines are no longer just passive tools—they’re active participants in the production process. For instance, a smart factory equipped with sensors can monitor the health of machines in real time, alerting operators when something is wrong before it turns into a costly breakdown. This is known as predictive maintenance, and it helps avoid downtime, saving companies time and money. By leveraging AI and machine learning, smart factories can also optimize production schedules, adapt to supply chain disruptions, and even reduce waste. Imagine that: a factory that’s not just smart, but also self-aware. It’s a total game-changer!
How Cyber-Physical Systems Enhance Manufacturing Operations
Cyber-Physical Systems are the stars of Smart Manufacturing, and their impact on operations is profound. By incorporating sensors, machines, and real-time data analytics, CPS helps manufacturers achieve precision and efficiency like never before. For example, a CPS-enabled robot can detect any abnormalities in the production process, such as a defective part or faulty material, and make immediate corrections without human intervention. This ability to detect, analyze, and act in real time significantly boosts production speed and quality control.
But the benefits don’t stop there! CPS also improves flexibility in manufacturing. In traditional manufacturing, adjusting production lines or changing product specifications often requires major overhauls. With CPS, however, factories can quickly adapt to new tasks or different product variations without disrupting the entire process. By automating decision-making and allowing machines to learn from each process, manufacturers can achieve a level of agility that’s simply impossible with older methods. These systems also enable seamless communication between machines and operators, creating a synchronized, efficient production environment that thrives on collaboration.
Applications of Cyber-Physical Systems in Smart Manufacturing
The applications of CPS in smart manufacturing are vast and varied. Industries such as automotive, electronics, textiles, and aerospace are already reaping the benefits of these innovations. Take the automotive industry, for example. Car manufacturers are using CPS to enhance their production lines by integrating robotic arms that are not just performing repetitive tasks but are also continuously monitoring and adjusting their movements for maximum efficiency. This creates a streamlined and highly efficient process, reducing errors and improving product quality.
Another exciting application is in supply chain management. With the integration of sensors and real-time data collection, CPS helps manufacturers track materials and finished goods throughout the entire production cycle. This level of visibility enables companies to manage inventory more effectively, avoid delays, and ensure timely deliveries. Plus, the ability to monitor the entire process from start to finish gives manufacturers valuable insights that can be used to optimize future production runs. The result? A more responsive, cost-effective, and agile manufacturing process that can keep pace with fast-changing markets.
The Role of Artificial Intelligence (AI) and Machine Learning in CPS
At the heart of CPS and Smart Manufacturing is Artificial Intelligence (AI) and Machine Learning. These technologies enable CPS to go beyond simple automation and truly optimize production processes. Through machine learning algorithms, machines can analyze large amounts of data and learn from past experiences to make better decisions in the future. This means fewer errors, better quality control, and more efficient production processes.
For example, in the case of predictive maintenance, AI can predict when a machine will fail by analyzing patterns in its behavior and comparing it to historical data. This allows companies to address potential issues before they cause downtime or costly repairs. Machine learning also plays a key role in demand forecasting, helping manufacturers predict customer demand and adjust production schedules accordingly. With the ability to analyze and adapt to real-time data, AI and machine learning make CPS-powered systems much smarter and more efficient.
Challenges and Considerations in Implementing CPS in Manufacturing
While the benefits of CPS and Smart Manufacturing are clear, the implementation of these technologies comes with its own set of challenges. For starters, the upfront cost of integrating CPS technologies can be high. Installing sensors, upgrading machines, and adopting advanced software solutions require significant investment. Smaller manufacturers may find these costs prohibitive, though they can still find ways to implement these technologies on a smaller scale as part of their digital transformation journey.
Another challenge is the complexity of integrating CPS into existing manufacturing infrastructures. Many legacy systems are not equipped to handle the demands of CPS, requiring companies to overhaul their operations or invest in costly upgrades. Additionally, as with any interconnected system, cybersecurity becomes a significant concern. With CPS linking machines, sensors, and data across an entire network, protecting sensitive information from cyberattacks is crucial. Thankfully, with the rise of cybersecurity technologies and awareness, manufacturers can take steps to secure their systems.
The Future of Cyber-Physical Systems and Smart Manufacturing
The future of Cyber-Physical Systems and Smart Manufacturing is incredibly bright. As technology advances, 5G networks, edge computing, and cloud platforms will only enhance the capabilities of CPS. 5G offers lightning-fast data transmission, which is ideal for CPS, as it allows real-time data to be processed instantly. Edge computing brings data processing closer to the machines themselves, reducing latency and improving decision-making times. With these technologies combined, the possibilities for Smart Manufacturing are limitless.
In the coming years, we can expect to see more personalized manufacturing solutions, where products are tailored to individual customers’ needs in real time. The integration of artificial intelligence, robotics, and big data will continue to push the boundaries of automation, leading to highly efficient, agile, and sustainable production systems. The future of CPS is not just about improving existing processes—it’s about creating entirely new possibilities for how products are made and how factories operate.
Conclusion
To sum it up, Cyber-Physical Systems are truly revolutionizing the world of Smart Manufacturing. By integrating digital intelligence with physical processes, manufacturers are achieving unparalleled efficiency, flexibility, and innovation. With AI, machine learning, and real-time data all playing pivotal roles, the future of manufacturing is set to be faster, smarter, and more sustainable than ever before. It’s an exciting time to be a part of this technological transformation, and the possibilities are endless!